This story starts in the Mediterranean Basin with family-owned businesses that aren’t too different from Heaven Hill Distillery.
Cork and whiskey are really not so different, you see. There are a few key ingredients that go into both a bottle of American Whiskey and the cork stopper you’ll find atop it. Terroir. Craftsmanship. Time.
Cork Oak
Harvest
It takes 25 years before a cork oak tree
can be harvested for the first time. After that,
the bark can be stripped every nine years.
However, it takes about 43 years before the
cork is high-enough quality for a bottle
stopper. These trees live 200 - 250 years
on average.
Sustainability
Cork oak forests sustain a rich biodiversity and play a key role in water retention, soil conservation and reduction of carbon emissions. For every ton of cork produced, on average about 73 tons of carbon dioxide are captured. From a social and economic sustainability standpoint, the forests have supported generations of farmers. In fact, growing and harvesting cork is the most well-paid agricultural work in the world, due to the expertise and care required.
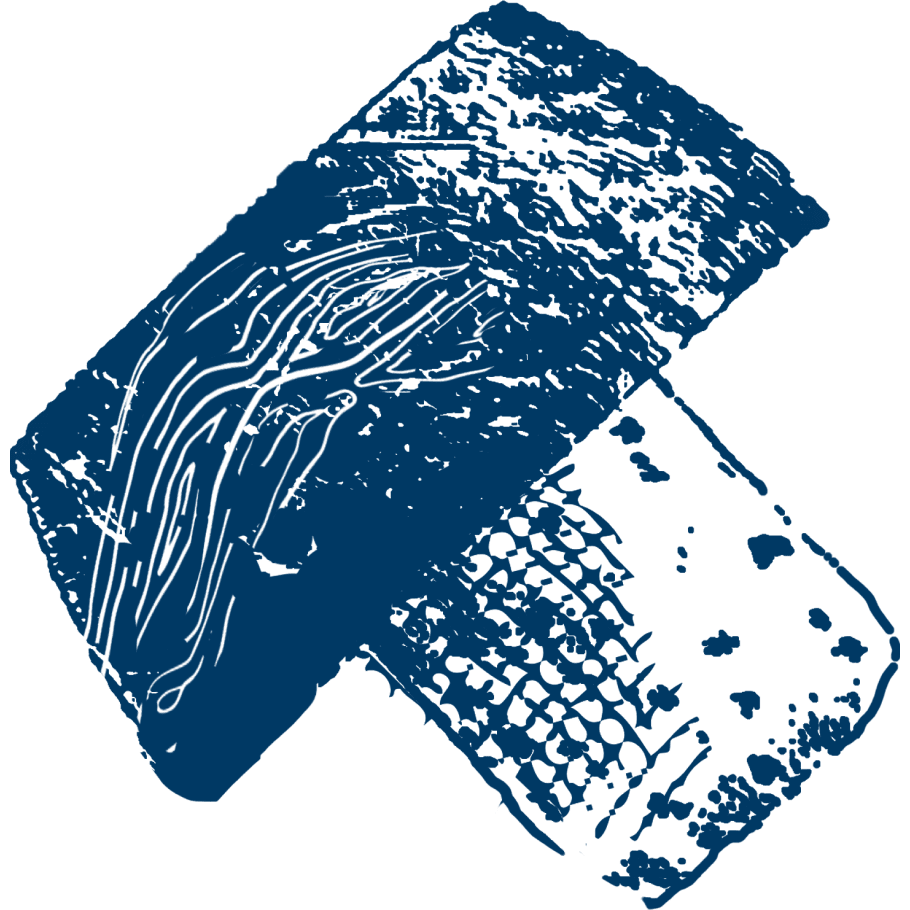
Sustainable
Recyclable
Biodegradable
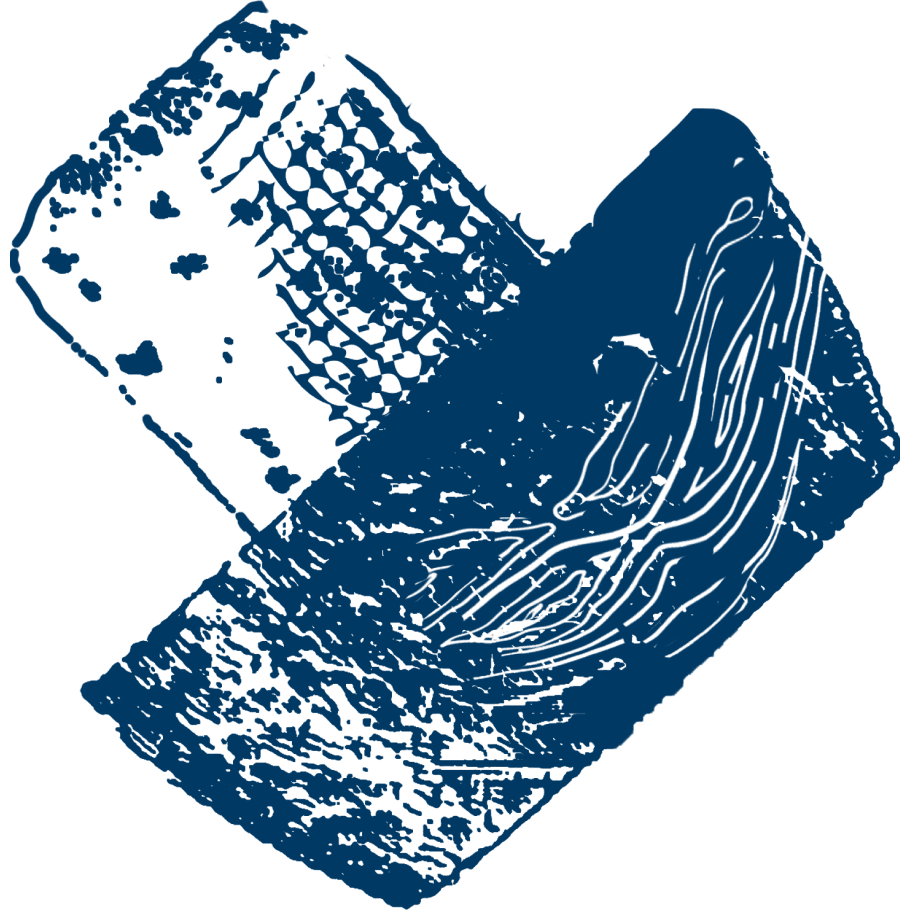
The Grading
Rundown
Because cork is an organic product, there is a natural variation in its quality.
There is also variation in how a cork plank, commonly known as raw material, is graded. Many suppliers have developed their own proprietary systems based on visuals. Lower grade cork has large pores—or holes called lenticels—throughout as well as cracks, wormholes, hardwood, belly spots and greenwood. This cork cannot be used to make whiskey stoppers but may be used for other applications such as flooring or insulation.
The smaller and fewer the lenticels, the higher the grade. Raw materials with a smooth texture, very few flaws and a dense appearance are typically used for bottling wine or spirits, as it creates a better seal and a smooth aesthetic.
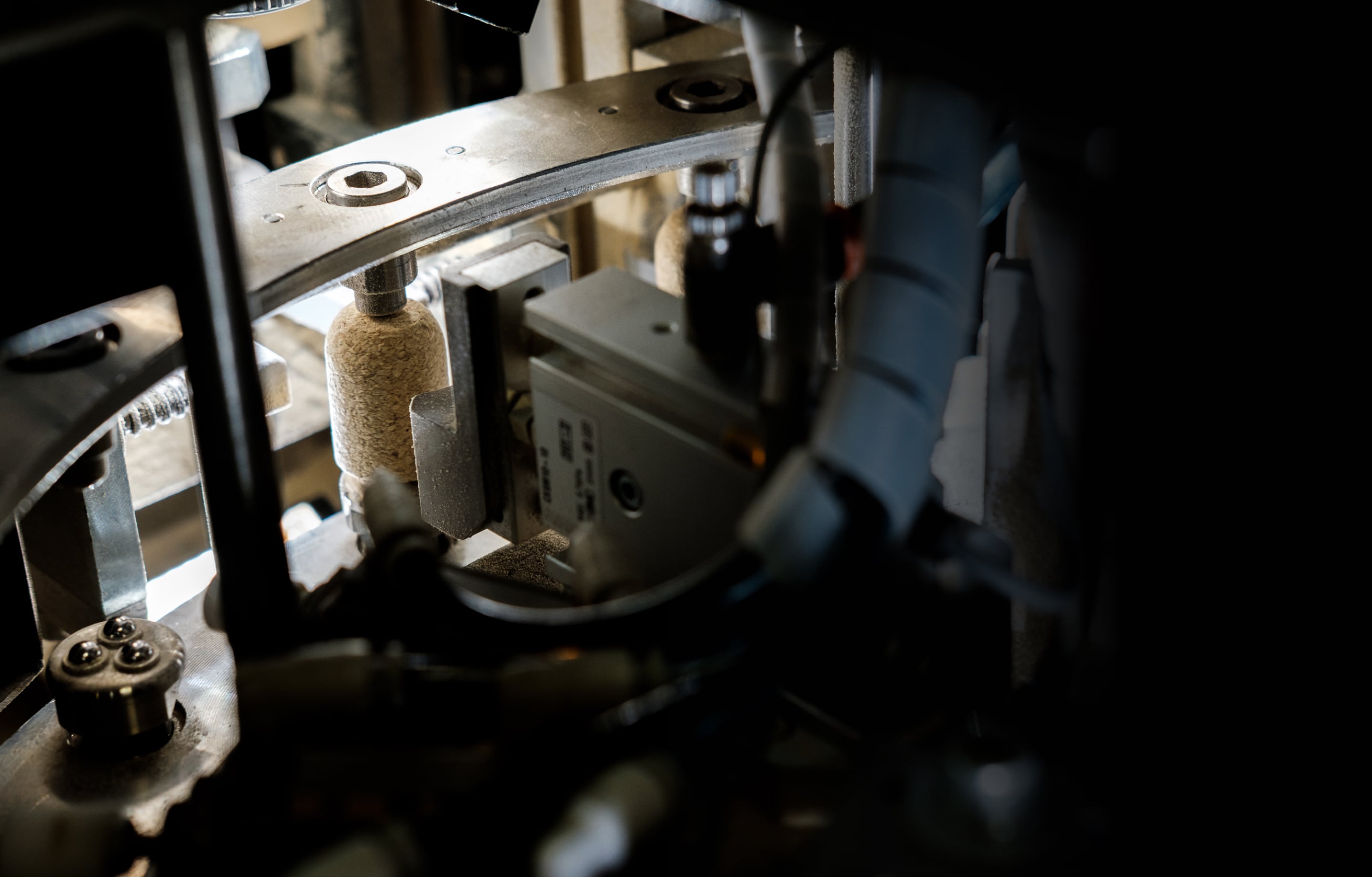
The process cork goes through is one that requires care and skill at each step.
And just like the process of making our American Whiskeys, it’s a mix of historic traditions, done by hand using knowledge that’s been passed down for generations, and new tools and technologies that ensure the final products are made to the highest standards.
1Harvesting
The harvest begins in May and runs through August. For this labor intensive process, harvesters use an axe and cut a ring around the trunk or branches. Stripped bark planks are carefully stacked and left to stabilize.
2Boiling
The cork bark is delivered from the forest to the boiling and punching operation. Here it is cut down to size and boiled. After boiling, the bark is flattened to form a plank that can be palletized. The planks are left to stabilize before punching.
3Punching
Boiled and stabilized planks are cut into strips. Cork shanks are then punched from the strips.
4Inspecting
Samples are taken from each delivery and evaluated. Shanks are then approved or rejected based on these results. After incoming lots are approved, shanks are placed in storage.
5Washing
Shanks are washed, sterilized and dried in preparation for sanding.
6Body Sanding
Next, shanks are sanded down to the final diameter. The ends of the shanks are then sanded to the final length.
7Sorting
After the shanks are sanded to the proper diameter and length, they are sorted using photoelectric imaging. Here, the sides and ends are inspected for quality.
8Chamfering
The best end of the cork shank is selected for chamfering. The edges are sanded down and beveled, creating a smoother rounded edge.
9Drying & Washing
All shanks are washed to remove dust and other loose material. They are then sent to a drying room to reduce their moisture content.
10Grading &
Metal Detection
After the shanks are stabilized to the correct moisture level, they are run through a metal detector to remove any ferrous or nonferrous metals. Then, the second sorting process takes place.
11Waxing & Silicone
Liquid wax and food grade silicone are sprayed on the shanks. These coatings allow for better application and removal.
12Grading Approval
& Assembly
Finally, tops are added to the cork and the shanks are finished.
Meet Our Partners
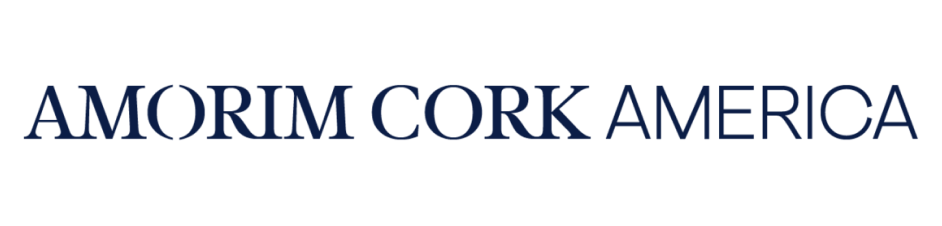
Founded in 1870 by the Amorim family, Amorim Cork has been at the forefront of the cork industry for over 150 years. With a strong commitment to sustainability and innovation, Amorim is known for its high-quality cork products produced using state-of-the-art technology and rigorous quality control standards.
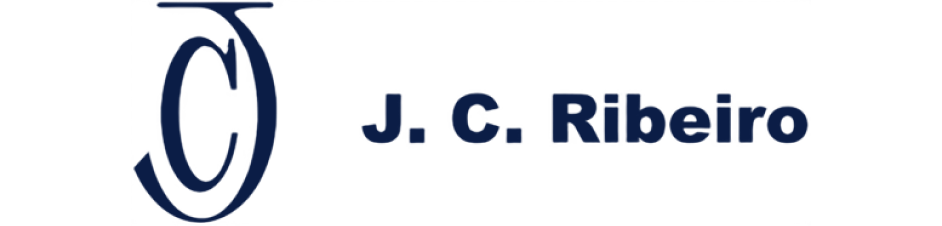
Founded in 1987, J.C. Ribeiro strives to meet the needs and challenges of the spirits industry. This family-owned company is devoted to the design, development and manufacture of high-quality cork stoppers with all kinds of materials for its tops.
Our Stopper
Showcase
Our whiskeys feature
a variety of bar
top stoppers.
This style is popular with spirits because it’s easy to reuse. That's important when the contents of a bottle typically won’t be consumed in one sitting. While the natural cork portion does its job keeping whiskey in your bottle and air out, the most recognizable part is the top. These can be made from a variety of materials and are highly customizable to suit each distinct brand.
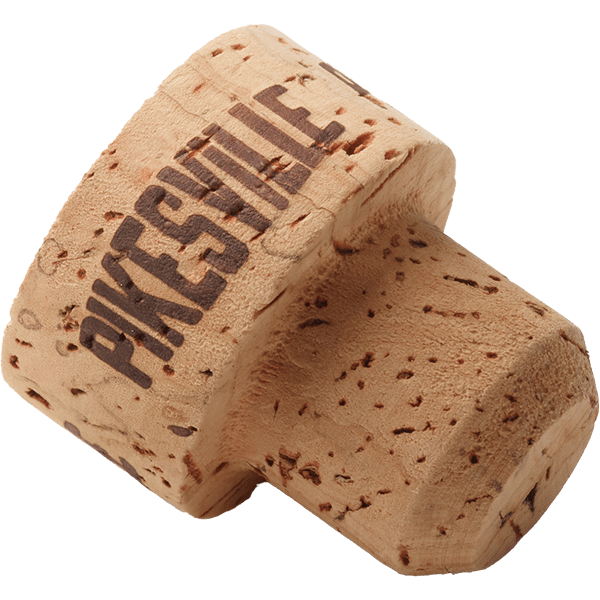
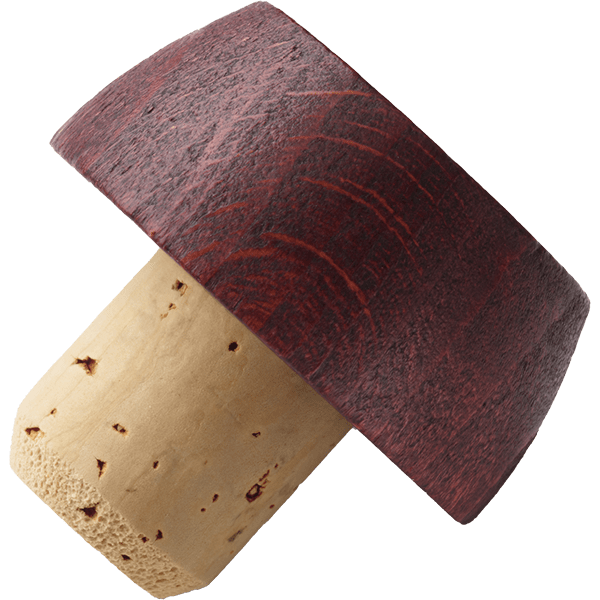
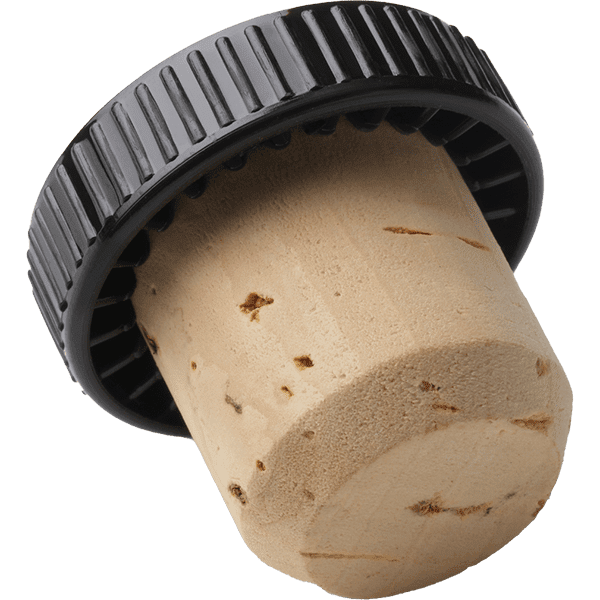
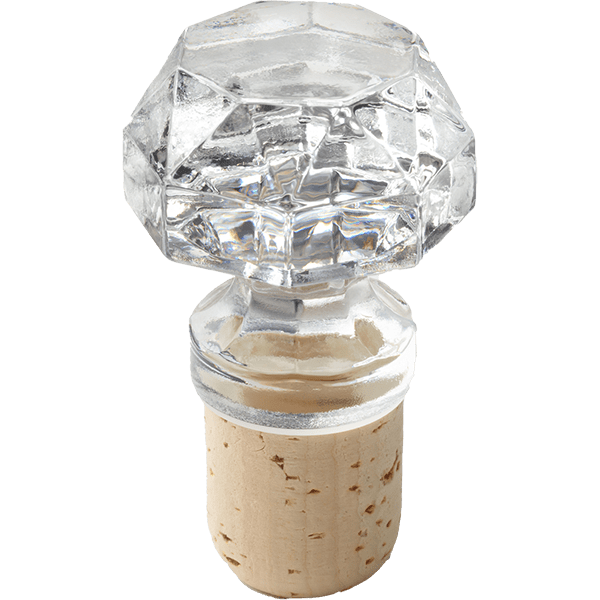
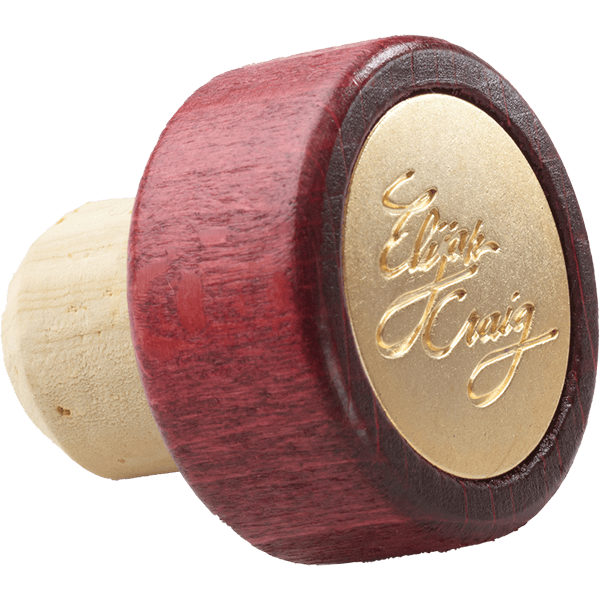
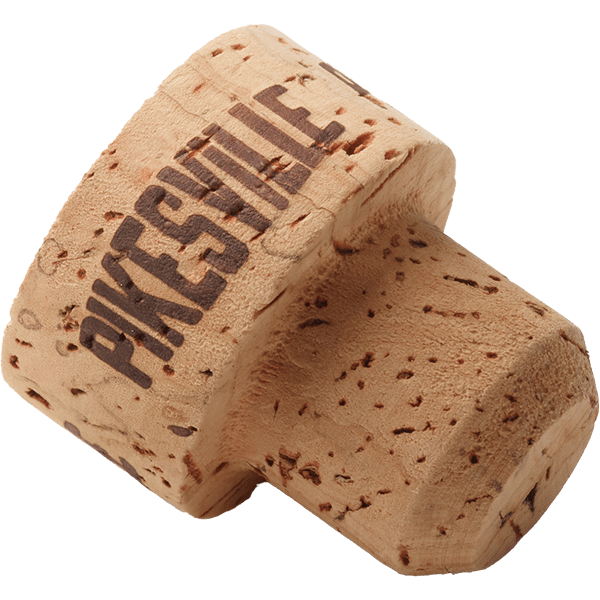
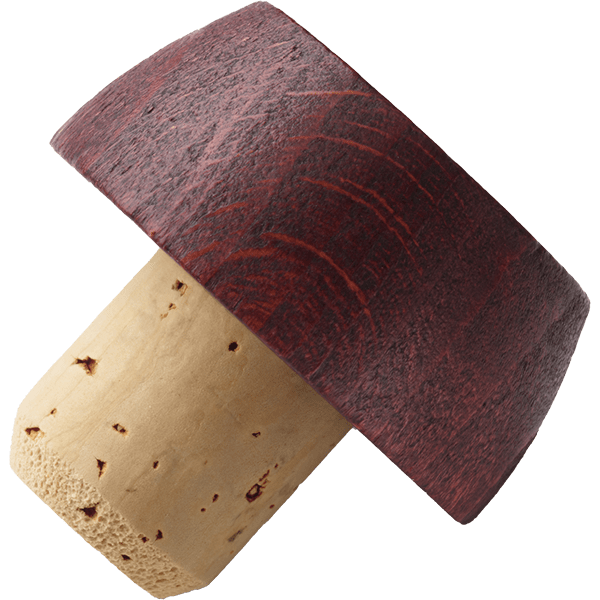
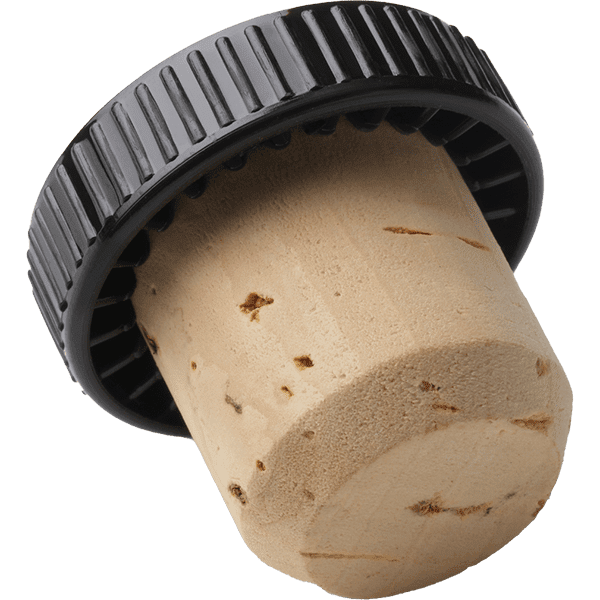
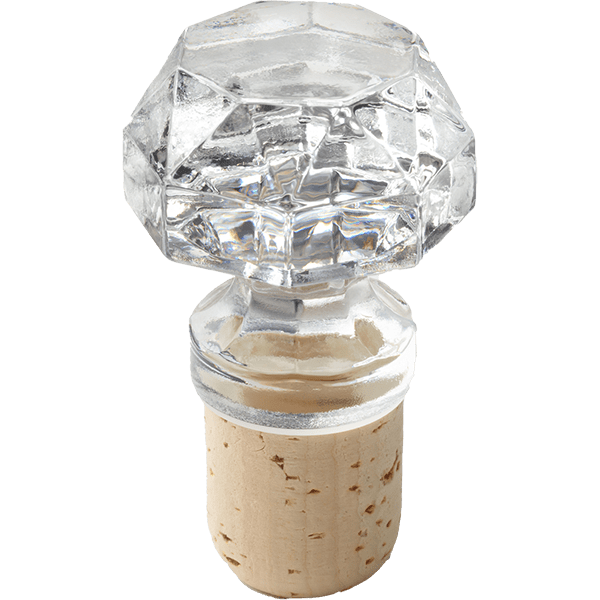
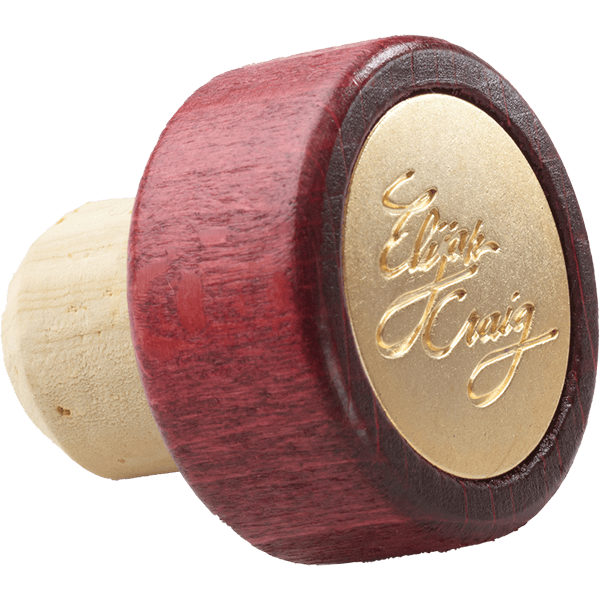
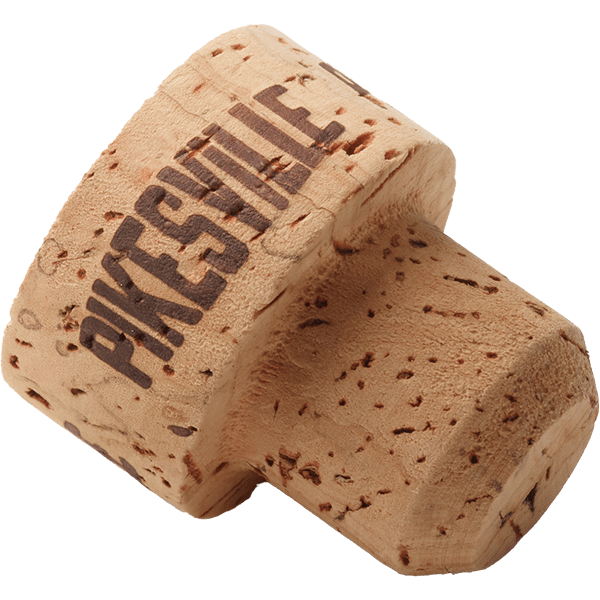
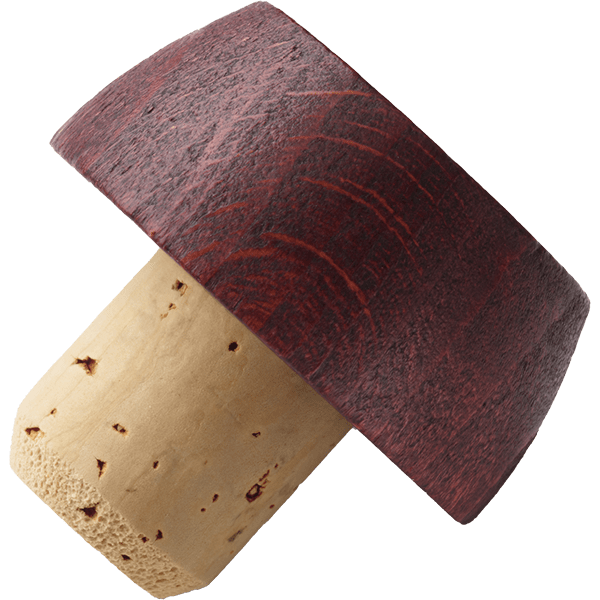
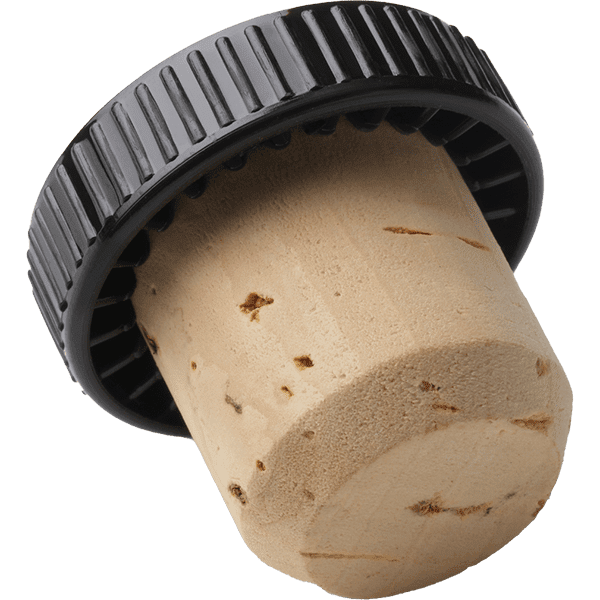
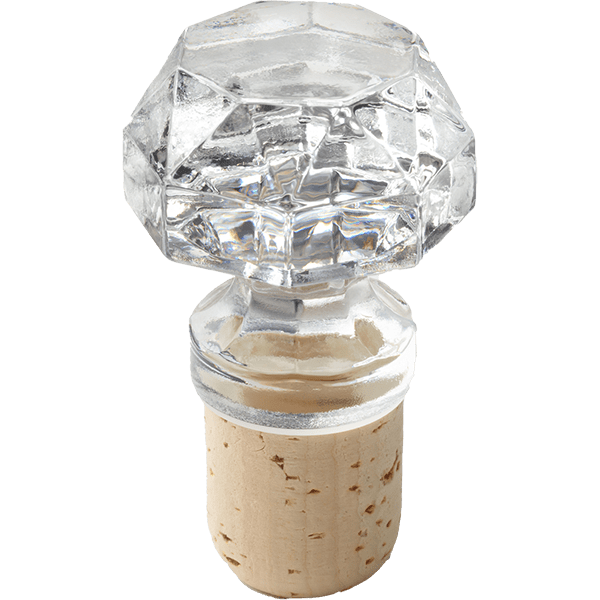
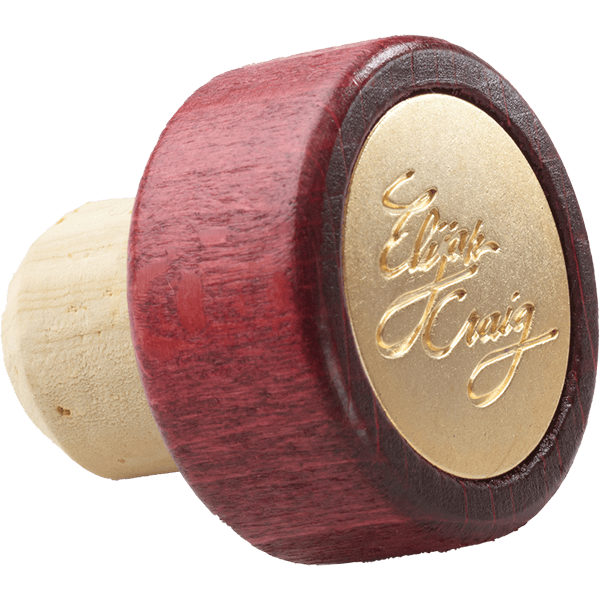
Cork
Pikesville Rye features a unique
all cork stopper
with the name
branded on sides.
Wood
Elijah Craig’s signature wood
stopper perfectly aligns
with the
bottle’s lip for a sleek appearance.
Plastic
This low profile plastic top lends
a streamlined look to
a bottle of
Bernheim Original Wheat Whiskey.
Glass
The design of Old Fitzgerald’s
glass-topped
stopper is inspired
by the brand’s original 1950s
diamond decanter.
Metal
Finishing off the top of this
collector’s bottle,
Elijah Craig 18
-Year-Old Single Barrel Bourbon
features a top with a metal inlay.
Cork
Pikesville Rye features a unique
all cork stopper
with the name
branded on sides.
Wood
Elijah Craig’s signature wood
stopper perfectly aligns
with the
bottle’s lip for a sleek appearance.
Plastic
This low profile plastic top lends
a streamlined look to
a bottle of
Bernheim Original Wheat Whiskey.
Glass
The design of Old Fitzgerald’s
glass-topped
stopper is inspired
by the brand’s original 1950s
diamond decanter.
Metal
Finishing off the top of this
collector’s bottle,
Elijah Craig 18
-Year-Old Single Barrel Bourbon
features a top with a metal inlay.
Cork
Pikesville Rye features a unique
all cork stopper
with the name
branded on sides.
Wood
Elijah Craig’s signature wood
stopper perfectly aligns
with the
bottle’s lip for a sleek appearance.
Plastic
This low profile plastic top lends
a streamlined look to
a bottle of
Bernheim Original Wheat Whiskey.
Glass
The design of Old Fitzgerald’s
glass-topped
stopper is inspired
by the brand’s original 1950s
diamond decanter.
Metal
Finishing off the top of this
collector’s bottle,
Elijah Craig 18
-Year-Old Single Barrel Bourbon
features a top with a metal inlay.
Want even
more cork
conversation?
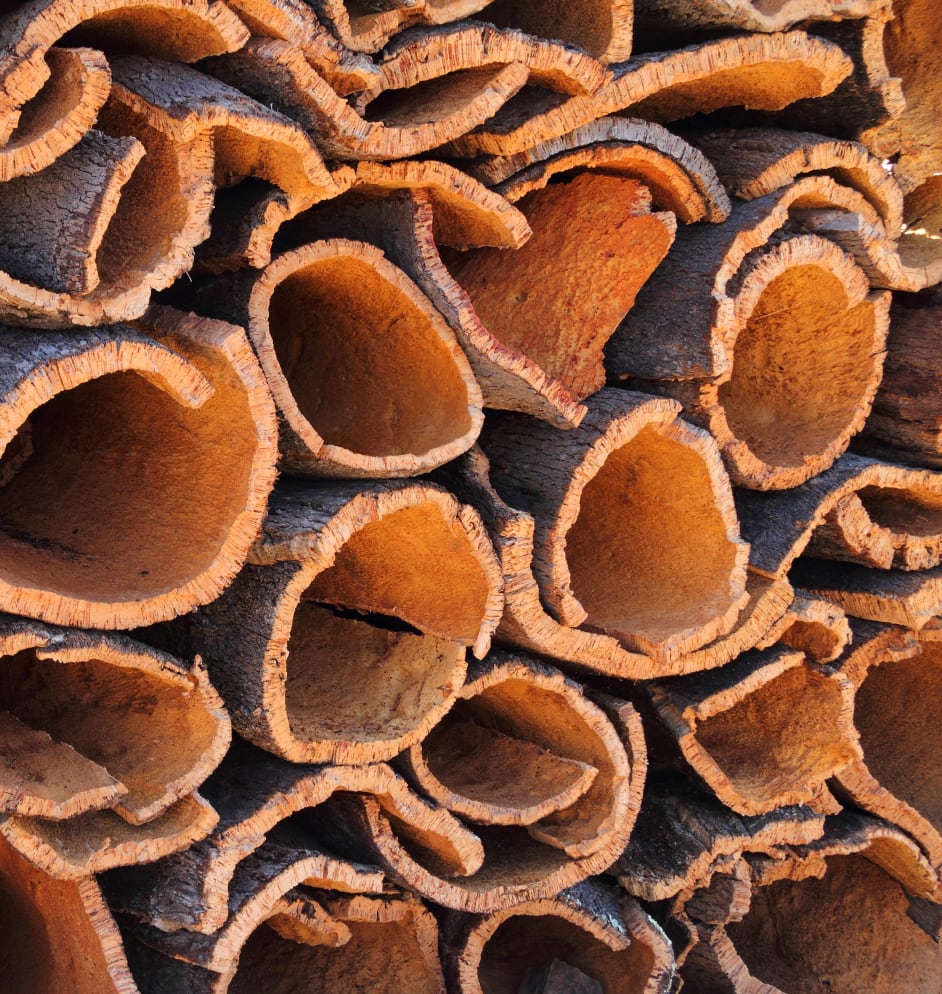
Want even
more cork
conversation?
On the Tales from the Hill podcast, we sit down with a group of experts to discuss all things cork, including how some of your favorite bottle stoppers came to be.